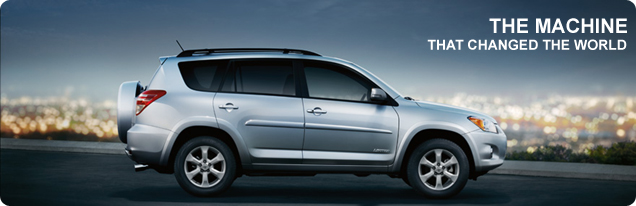
Periodic physical count of inventory
• A physical count of items in inventory at a periodic intervals (Annually - Quarterly - Monthly ) in order to decide how
a. Why Is a Physical Inventory Necessary?
Contributes to Better Customer Service. It is to verify that the on-hand quantity of each item in your computer reflects what is actually on the shelf.
Is Necessary for Effective Replenishment. If On-hand Quantities in the computer are not equal to are actually in the warehouse the wrong quantities, of the wrong products, will be ordered.
b. Planning for a Good Physical Inventory
Set the count date(s) as early as possible so that everyone has plenty of notice. If you have several locations, but limited management personnel available to supervise the counting process, consider counting each branch on a different date.
Select the method you will use to conduct the physical.
Bar-Code Readers.
Count Cards. Count cards (index cards containing an individual product and bin location)
Count Sheets. Count sheets (8-1/2" x 11" pieces of paper each listing about 25 inventory items)
Determine who will count. If you are using bar code equipment, one person can count a section of your warehouse. But if you are using count cards or sheets, it*s often better to have two person counting teams.
Order the necessary supplies. Determine what you will need to obtain to conduct your inventory count. Supplies may include count cards, bar code readers, clipboards, and computer paper.
Clean up your warehouse. and make sure that every piece of every item is where it belongs before the counting process begins.
c. How to effectively administer the actual counting process.
Create a map of your warehouse 每 Include every shelving unit, pallet rack, and all other places where material is stored.
Divide the warehouse into counting areas
Counters should be assigned to geographic areas of the warehouse, not product lines.
When establishing count areas, remember that a count team should normally be able to count between 50 and 120 items in an hour.
Hard-to-count products, such as those that need to be weighed or closely examined, take more time.
Consider counting surplus areas and slow-moving products before the scheduled physical inventory
The possibility is small that significant amounts of your dead stock, slow moving inventory, and surplus material will move during the week preceding your physical.
Be sure to mark bins and shelves that are pre-counted.
You must have some mechanism for adjusting these quantities if some amount of a product is sold or received after the bin has been counted.
Ship everything you can before the physical begins
Update computer records for receipts, sales orders, and transfers.
Process all customer returns and return material to stock.
Don*t move misplaced material while you count
Don*t fill orders or receive material during the count process 每 the auditor must determine how the emergency order affects the physical.
Audit while people are still counting
As soon as counters are finished with a small section of bins or shelves, an auditor can verify the counts of selected products.
Don*t choose these products at random; instead, concentrate on your "A" items. These are the items that have the most dollars flowing through inventory.
Print and review discrepancy reports
Errors may also result from things that are not related to the actual counting such as:
• Mistakes made as counts are entered into the computer.
• Unit-of-measure errors in computer records. For example, a product may be counted in pieces, but maintained in the system in pounds.
Discrepancy reports should list any item with a significant difference between the on-hand balance in the computer (before the physical) and the counted quantity.
Good discrepancy reports highlight items with significant differences in value (i.e. differences in the on-hand quantity times cost).
Review your success, record your procedures
What worked? What didn*t?
Who should perform what tasks next year?
What could be changed to make things easier and produce a more accurate count?
d. Disadvantages physical count
Expensive
Shut down production / shipping 每 sometimes for days
Unidentified or misidentified material
Inexperienced, reluctant counters
Temptation to cut corners
Missing documents
Count, recount, audit counts
Cannot track down causes of errors
Often introduces more errors than it fixe
Cycle Counting Program
• In order to receive all of the benefits from a good inventory management system, stock balances must be at least 97% accurate, every day of the year.
• To ensure that a minimum of 97% accuracy is maintained is to continually count your products. That is, count part of your inventory every day, and count each item several times per year. This process is called "cycle counting."
• The problem of Material Movement makes cycle counting more difficult than a complete inventory. That problem is material movement.
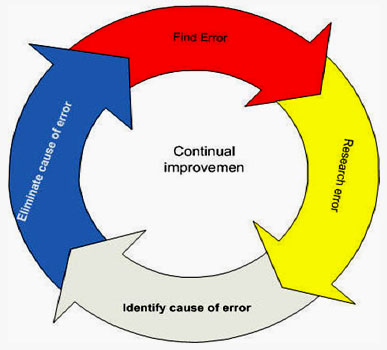
a. Common Causes for Errors
• counting procedure/equipment
• untrained personnel
• carelessness
• poor forms design
• poor document control
• inventory adjustments
• lack of transaction discipline
• midnight requisitions
b. Deciding What to Count
• ABC analysis
• Location counting
• Negative on-hand items
• When order placed
• When order received
• Today*s problems
• Control Group
c. Deciding How Often to Count
• ABC
• After specified number of transactions
• What*s possible with staffing level
d. Guidelines for a cycle counting program
• Decide which cycle counting method to use
The Geographic Method
facilitates the "discovery" of misplaced or lost material
try to count each stocked item at least four times per year.
The Ranking Method "Pareto*s Law"
"A" rank items (responsible for the top 80% of sales) count six times per year
"B" rank items (responsible for the next 15% of sales) count three times per year
"C" rank items (responsible for the next 4% of sales) count twice per year
"D" rank items (responsible for the last 1% of sales) and products with no sales count once per year
Most distributors prefer the Ranking Method.
• When should cycle counting be performed?
Some time during the day when material "off" hours. (one hour each morning before your warehouse opens for business or an hour each afternoon, after the last order has been filled)
• The Number of Items Counted each Day
If you use the geographic cycle count method, and have 10,000 items in inventory, you will have to count about 160 products per day:
10,000 items counted four times per year = 40,000 counts
40,000 counts / 250 days = 160 products counted per year
Experienced person can usually count between 100 and 150 products in an hour.
Using the Ranking Method the distributor of the 10,000 stocked items could be:
• Rank "A" contains 2,000 products
• Rank "B" contains 3,000 products
• Rank "C" contains 4,000 products
• Rank "D" and the dead stock category contain 1,000 products
2,000 "A" items counted six times per year = 12,000 counts
3,000 "B" items counted three times per year = 9,000 counts
4,000 "C" items counted twice per year = 8,000 counts
1,000 "D" items counted once per year = 1,000 counts
Total 30,000 counts
30,000 counts / 250 counting days = 120 products counted per day
Ranking Method requires fewer products to be counted each day and results Greater inventory accuracy.
• Determine who should count. only knowledgeable, experienced warehouse people.
• Develop Your Count Schedule
For a geographic program, Start at one end of your warehouse, assign the first 160 products to "Day 1," the next 160 products to "Day 2," and so on.
Unless you have a computer system that can maintain multiple on-hand quantities for an item, you should count all locations for an item on the day that item is scheduled to be counted.
For a rank-based cycle counting program be sure that your stocked products are re-ranked (based on annual cost of goods sold) on a regular basis.
Here is a rank-based cycle counting schedule for the distributor that will attain the desired number of counts for each product. Note that on some "transition days" items from two groups will be counted:
Day 1-17 Count "A" items
Day 18-42 Count "B" items
Day 42-59 Count "A" items
Day 59-74 Count 1st half of "C" items
Day 75-91 Count "A" items
Day 92-116 Count "B" items
Day 117-133 Count "A" items
Day 134-149 Count 2nd half of "C" items
Day 150-166 Count "A" items
Day 167-174 Count "D" items
Day 175-199 Count "B" items
Day 200-216 Count "A" items
Day 217-250 Count "C" items
• Reconciling Cycle Counts (adjustment of Shelf counting)
Sales orders that have been filled, but have not been confirmed in the computer. The confirmation process reduces the on-hand quantity in the computer by the quantity shipped on the sales order. If a customer order or outgoing transfer has been filled but not confirmed, the quantity shipped of the item must added to the quantity physically counted before that amount is compared to the on-hand figure in the computer.
Stock receipts entered in the system, but not yet placed in the proper bin location. Again the quantities on these stock receipts must be added to the counted quantity before being compared to the on-hand amount in the computer.
Stock receipts placed in the proper bin location, but not yet entered in the system. These amounts must be subtracted from the counted quantity before that amount is compared to the on-hand quantity in the computer.
"Floating" paperwork is the most common reason for cycle count discrepancies. To facilitate the count process, it is a good idea for counters to receive a list of open transactions for the items being counted each day.
How to Start a Cycle Count Program
• Step 1. Controlled Test
a. Pick 100 representative parts
b. Divide into 25/day 每 Mon thru Thursday
c. Friday for clean up
d. Begin with accurate count
e. Note and investigate variances each day
f. Keep track of daily accuracy percentage (spreadsheet)
g. Cycle Counter uses checklist to investigate possible root causes
h. After finding root cause, correct inventory record (spreadsheet)
i. Record of cause, who will fix and when
j. Keep checking until you*ve attained 100% accuracy for two or three weeks (Predictable results)
k. If time available, also check negative on-hand items
• Result of Step 1
You have begun to establish the discipline necessary to maintain an accurate inventory
You have identified and corrected most of the errors that are causing inaccurate inventories
• Step 2. An Expanded Test
1. Expand to a larger number of items (600 to 700?)
2. Use ABC categories
a. count bimonthly
b. count monthly
c. count quarterly
3. Keep inventory accuracy and cause records (spreadsheets)
4. Continue until you*ve attained 100% accuracy for two or three weeks (Predictable results)
• Step 3 每 Full Cycle Counts
Once the root causes are identified and are being dealt with for the items in the Expanded Test, and the Cycle Counting procedures have been reviewed and are in place, the Cycle Counting program should be expanded to include all of the inventory items.
You can achieve 97%+ accuracy
If accuracy level maintained long enough 每 you may be able to eliminate periodic physical inventory counts
» More Information